Autoclave Composite is the key equipment mainly used for hot press curing of metal/non-metal bonded structural parts and resin-based high-strength glass fiber, carbon fiber, boron fiber, aramid fiber and epoxy resin composites. The device can realize heating and pressure curing molding under the condition that the composite material is evacuated.
Autoclave composite is also the indispensable process equipment for forming polymer matrix composite products. The forming process of hot pressing tank is to seal the composite blank, honeycomb sandwich structure or adhesive structure in a vacuum bag on a mold and put it in a hot pressing tank. Under vacuum or non vacuum condition, the process of pressure protection and temperature reduction through heating, pressure and heat preservation (medium temperature or high temperature) can makes the work piece into predefined shape and mass shape. Autoclave composite molding technology is one of the main forming methods for composite materials, honeycomb sandwich structures and metal or composite adhesive structures widely used. When the material is formed, the curing can be achieved by the uniform temperature and pressure environment provided by the hot pressing tank, so the quality of the surface and the interior is high, the structure is complex and the area is huge.
The curing of matrix composites is related to the molecular structure of resins and other components (curing agents, cross linking accelerators, etc.). The external conditions such as temperature, pressure and time factors are called the three factors as the main technological parameters in the curing process. All hot pressing tank molding methods should determine the corresponding technological parameters according to the molecular structure change discipline of the matrix resin. The hot pressing tank must have the function to control the process parameters.
1. Autoclave Composite Performance
Our autoclave tank temperature, pressure and vacuum control are in line with the Boeing BAC5621 “K”, D6-56273 “B”, D6-49327 “E” and AMS2750 “D” process standards.
The autoclave produced by our company can achieve the unity of the vacuum bag inside the work piece, the mold and the air temperature in the tank, effectively control the temperature difference in different parts of the work piece, the working temperature difference can be controlled at ± 0.5 °C
2.1 Example recipe of autoclave composite
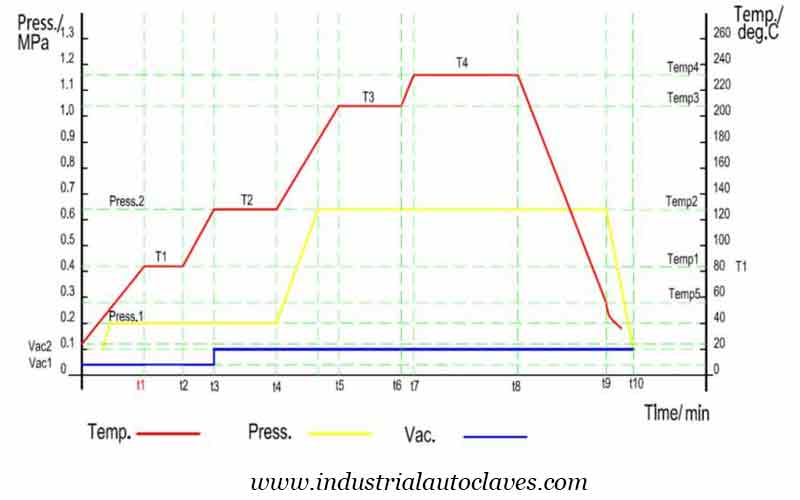
How to operate Autoclave Composite
Vacu1: minimum vacuum pressure Vac2: maximum vacuum pressure
Press.1: Pr-pressure Press.2: final pressure
Temp1:temperature of first segment Temp2: temperature of second segment
Temp3: temperature of third segment Temp4: temperature of forth segment
Temp5: temperature of cooling and release
T1: keeping time of first segment T2 : keeping time of second segment
T3: keeping time of third segment T4 :keeping time of forth segment
2.2 The superiority of the autoclave composite control system
- Easy to operate: One-button automation process control (can be unattended).
- System Control Reliability: Uses high quality and high performance control components (ensuring the reliability of the control system).
- Advanced curing control concept: single device and multiple device control (to achieve system redundancy and DCS distributed control).
- Big data acquisition: data acquisition, storage, printing, comprehensive report.
- Automatic quality analysis: With fluid mechanics software, can help users to carry out simulation analysis.
- Multilingual operation interface: Allows you to switch interface language at any time.
- System sensibility: user-friendly development and resource integration
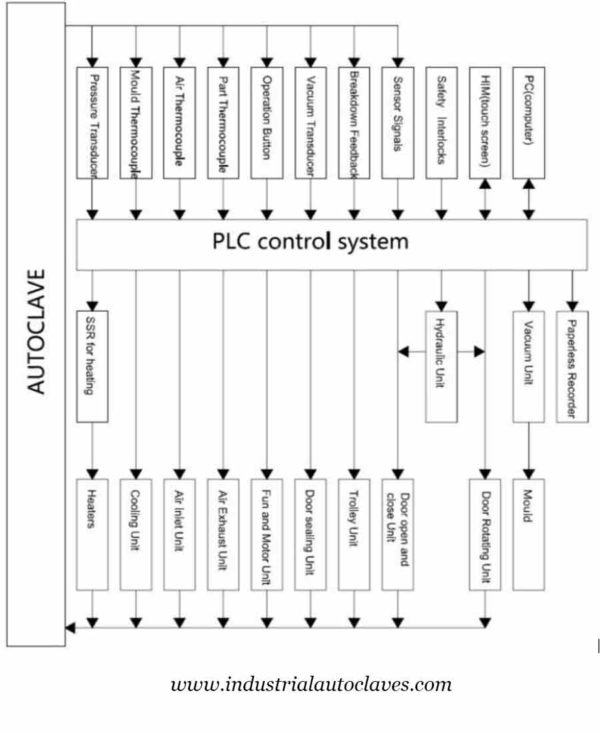
How to Operate Autoclave Composite
3. Safety and reliability of autoclave composite
- The autoclave composite tank is equipped with a safety valve. Under the normal working pressure of the autoclave tank, it maintains a sealed state. When the pressure in the tank exceeds the opening pressure of the safety valve, the gas is automatically opened and discharged. When the pressure drops to the specified value, it is automatically closed. Keep working properly to protect the safety of the tank.
- The autoclave composite pressure is automatically controlled. When the pressure in the tank reaches the set value, the regulator valve is automatically turned off. When the pressure exceeds a certain value, the exhaust valve automatically opens the exhaust gas to the set pressure value.
- The autoclave composite pressure tank is equipped with over pressure and over temperature sound and light alarm
- The safety device is set to perform zero-pressure check of the pressure inside the tank during opening to prevent the remaining pressure from hurting people.
- The device uses electrical interlock to prevent misuse
- Safety function: the tank door’s turn off and over pressure alarm chain, the tank door’s turn on/off and the safety connection device chain, the tank door switch and the tank door swing open chain, the tank door turn off and pressure chain, the fan runs With the cooling water / fan temperature switch chain, pressure control and the tank door seal air chain, heating and fan chain and so on. These interlocking functions are automatically protected even if an error occurs.
4.Autoclave Pressure Vessel
4.1 Fabrication Standard of Autoclave Pressure Vessel
Autoclave pressure vessel with quick-opening door, can be certified to:
- CHINESE STANDARD,GB 150-2011
- AMERICAN STANDARD ASME SEC VIII DIV.1 with ASME Certificate
- EUROPEAN STANDARD PED 97/23/EC with PED
Here listed specifications of carbon fiber autoclave for sale :1.1 Main specification
UNITE
CONTENT
DOOR CAP PCS 1 INTERIOR DIA mm 4400 WORK LENGTH mm 15000 WORK PRESSURE MPa 1.5 WORK TEMPERATURE ℃ 400 BODY MATERIAL SA516.Gr70/SA266GrB INTERIOR INSULATION INTERIOR HEATING Electrical coil COOLING MEDIUM Water USAGE Hot press curing LOADING WEIGHT Kg 15000 TEMPERATURE RISING RATE ℃/min 0.1-5(NON-LOADING) COOLING RATE ℃/min 0.1-5(NON-LOADING) COOLING TEM. LIMIT ℃ 60 TEM. UNIFORMITY ℃ ±2℃(NON-LOADING) THERMORCOUPLE NOZS. 48 EXTERIOR SHELL TEM. ℃/min +20 room temperature, non – over than 50 PRESSURE CONTROL ACCURACY MPa 0.02Mpa PRESSURE RISING RATE MPa/min 0-0.05Mpa PRESSURE RELEASE RATE MPa/min 0-0.005Mpa SILENSER GRADE dBA ≦80 1.2 Basic design ENVIRONMENT WORKING TEMPERATURE ℃/min 5~45℃ POWER VOLTAGE V 400V FREQUENCY Hz 50 PENUMATIC PRESSURE MPa 0.8 PENUMATIC REQUIREMENTS Non-oil, -5℃, CIRCULATION WATER PRESSURE MPa 0.3 1.3 Air circulation AIR FLOW Circle MOTOR QUANTITY 1 MOTOR POWER KW 120 1.4 Heating system HEATING Electric heating COILS NOZZS Pc 1 COIL MATERIAL Stainless steel HEATING POWER KW 1400 1.5 Cooling system COOLING MEDIUM Water COOLER NOZS SET 1 COOLER MATERIAL Stainless steel 1.6 Pressure system ( By Customer) GAS TYPE Nitrogen GAS PRESSURE MPa 4.0MPa AIR COMPRESSOR Kw 90KW Nitrogen production M³/h 800 Cold and dry machine Compatible with air compressor Gas tank M³ 160 Gas tank pressure MPa 4.0 1.7 Circulation water(By Customer) WATER GRADE SOFT WATER PUMP 50m3×2 WATER TANK 30m3×2 Cooling tower 50 m3/h 1.8 Vacuum sytem VACUUM PORTS NOZS. 24 LIMIT VACUUM GRADE Mpa -0.098MPa VACUUM MOTOR Rotary vane pump - Specification in detail of autoclave composite
1)Temperature: Maximum working temperature: 400ºC ambient to the maximum temperature with empty load.
2) Heating rate:1‐5ºC/min based on average air temperature from
3) Cooling rate:0.1‐5ºC /min based on average air temperature from maximum temperature to 60ºC with empty load.
- 4)Steady‐state temperature control accuracy: ± 2ºC
- 5)Pressure:Maximum working pressure: 1.5MPa
- 6)Pressurization rate:0-0.05MPa/min
7)Steady‐state pressure control accuracy: ±0.014MPa
- System introduction of autoclave pressure vessel
3.1 Flange cap of industrial autoclave manufacturers
1)Flag swing. Hydraulically operated door with side ward open.
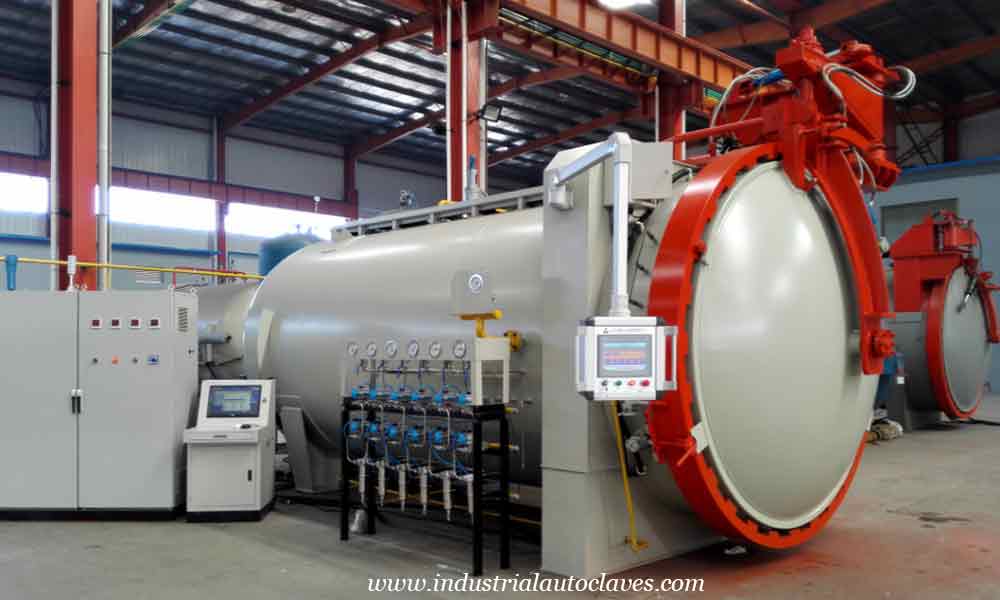
How to Operate Autoclave Composite
3.2 Body of autoclave composite
1) Adopt SA516 Gr70 mid-steel2)Paint:Autoclave will be primed and painted color according to customer required; here it is cool-gray in paint
3)Approximate shipping weight:105,000 KG.
4)Tank color blue, yellow (customer provides color code)
3.3 Insulation of autoclave composite
1)Interior insulation structure 2)Internal sheet metal: Insulation liner, 304stailess steel3)Insulation:Mineral wool insulation: 150mm. Ceramic aluminum silicate ceramic folding cotton
4) High density insulation which is environmental material
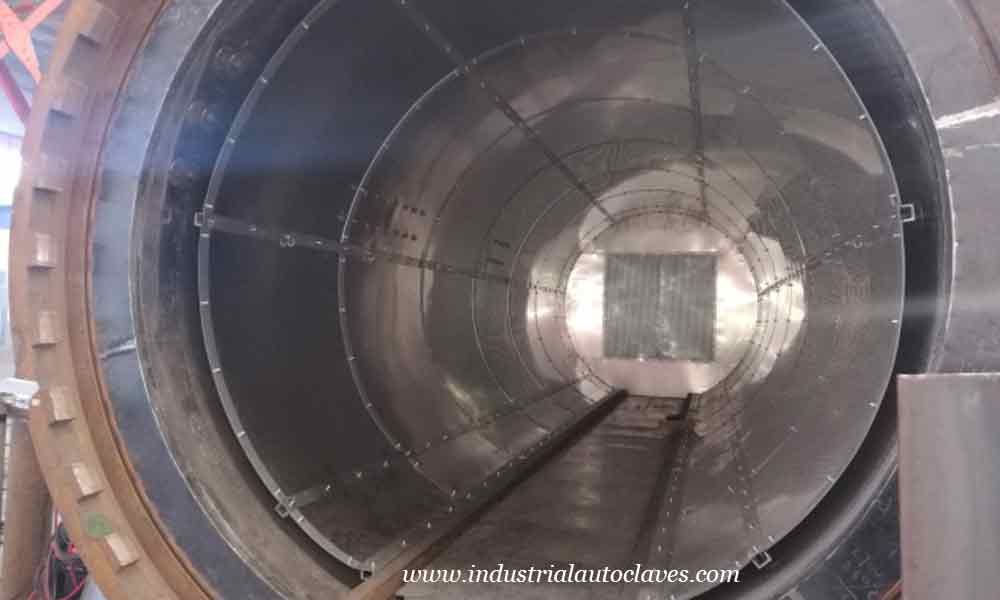
How to Operate Autoclave Composite
3.4 Loading design of large autoclave
1)Floor supports rails
2)Loading: 15000 kg
3)Cart:Full length cart with 10000kg loading capability
3.5 Motor& fans air flow of autoclave composite
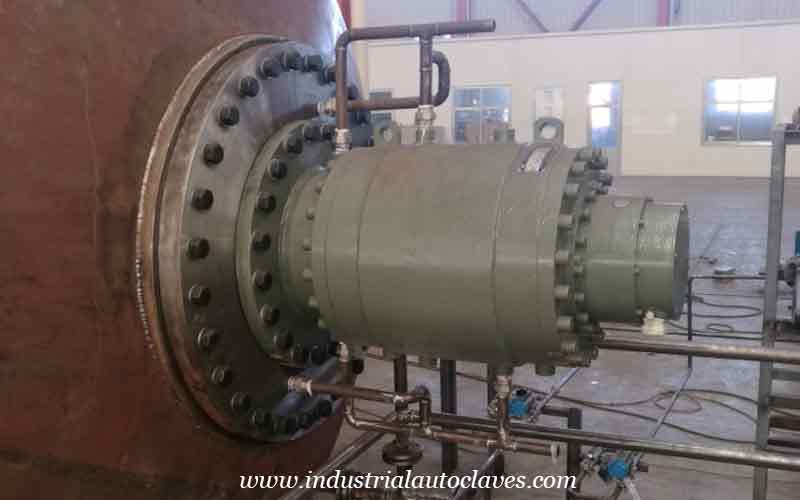
How to Operate Autoclave Composite
1)Fan Motor: 120KW, 415V, 3PH – 50 Hz
2)Motor mounting: Capsule with water cooling
3)Motor jacket cooling system
4)Flow‐switch indication to PC
3.6 Heating control of autoclave pressure vessel
1)Electric heating via innocent (Stainless steel ) tubular heaters:
2)Heaters are mounted back at end of autoclave with moving wheels for easy system maintenance.
3)Estimated Heater size: about 1400KW
4) Two linear regulator for heating power , each unite guarantee heating work efficient and energy saving.
5)SSR banks with safety contractor.
6)Proportional control 0‐100% output
3.7 Cooling system of autoclave composite
1) Stainless‐steelheatAll internal wetted parts stainless steel
2) Ex changer mounted below floor for easy system maintenance.
3) Proportional cooling valve for main cooling control.Computer controlled.
4) Air spray and Mist water valves for trim cooling control.Computer controlled.
5) Water consumption of cooling tower : 50m3/h.
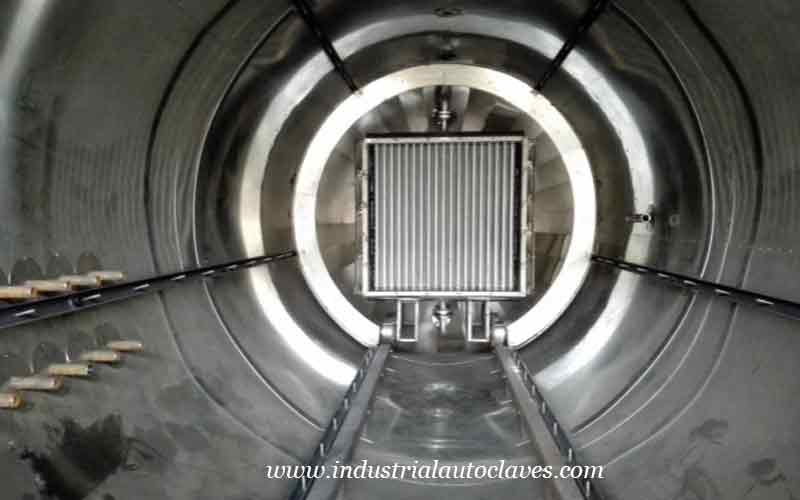
How to Operate Autoclave Composite
3.8 Pressure control of autoclave composite
1)Automated Inlet and exhaust valve, stainless‐steel construction
2)Manual exhaust valve, stainless‐steel construction
3)Exhaust silencer (Outside of room be ok)
4)Pressure transducer:2
5) Accuracy: ± 0.25%
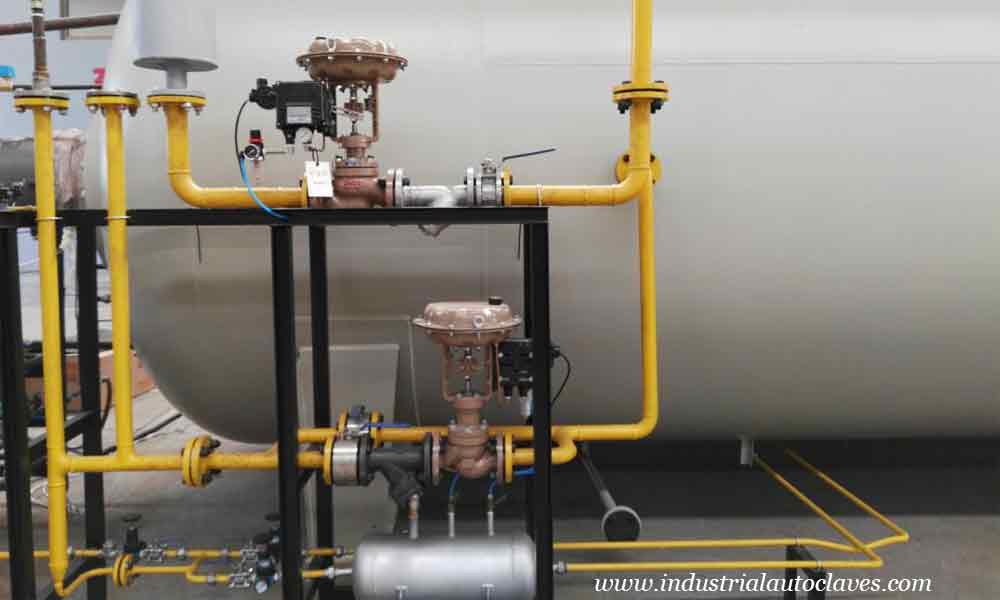
How to Operate Autoclave Composite
3.9 Vacuum system of large autoclave
1)Vacuum source ports: 24 total
2)Each source port will include: 1/2” NPT pipe feed through
3)External manual blocking valve, 3‐piece ball valve, stainless‐steel
4)Stainless‐steel tubing, 1/2”
5)Block Valve on each pipe.
6) Accuracy: +/‐ 0.25%
7) Vacuum pumps: quantity 2, flow rate of each one: ≥100m³/h. Pumps will be Selectable from control computer for four modes of operation:
8)Vacuum pumps can works on 4 models:
9.1 ) Pump #1 operation only
9.2 ) Pump #2 operation only
9.3) Both pumps on simultaneously.
9.4) Automatic switching between Pump1 and Pump2 every 24 hours.
10)A controlled vacuum level reservoir, and vacuum level is adjustable.
11)All piping and valves of vacuum system are stainless steel.
How to Operate Autoclave Composite
3.10 Temperature measurement unit of autoclave composite
1)Air temperature thermocouples: 48
2)Ω‐K, including computer monitoring/control.
3)Ω‐K, including PC monitoring, data‐acquisition, and control
4)Measurement precision: +/‐1.1C
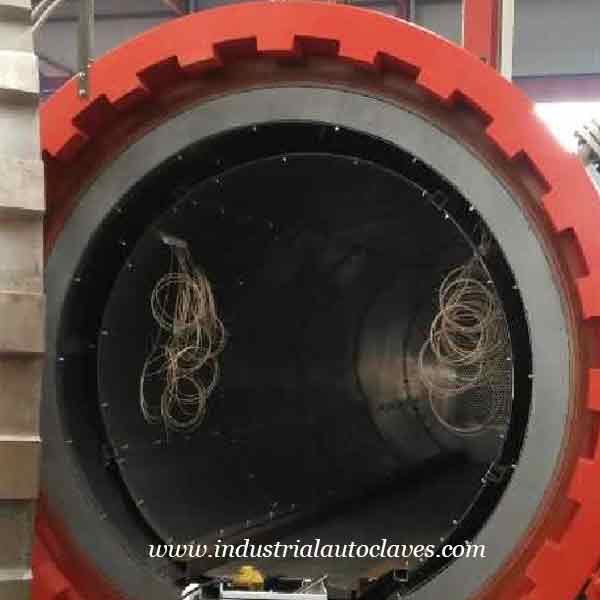
How to Operate Autoclave Composite
3.11 Safety part of autoclave composite
1)Pneumatic, mechanical, and electrical interlocks for door closure
2)High temperature controller with alarm/interlock
3)Pressure safety relief valve, Nozzle according with the ASME standard
4)Oxygen monitoring system interlocked to the Econoclave door safety lock to prevent opening of the door until a safe oxygen level is achieved.
3.12 Automatic operation system
1)1 each business PC’s , Current Intel™ processor (Over Intel Core i3/i5/i7), fully loaded with CPC™,22” Flat screen monitors &1
2)UPS, 500VA. Connected to the PLC and both PC computers
3)Allen Bradley switches, buttons, lights, etc.
4)Power system components
5)Ne ma‐12 enclosure Main circuit breakers, standard interrupting
6)Motor starters, Schneider
7)Contractors, Schneider
8)Thyristor/SCR: Chromalox by PID control.
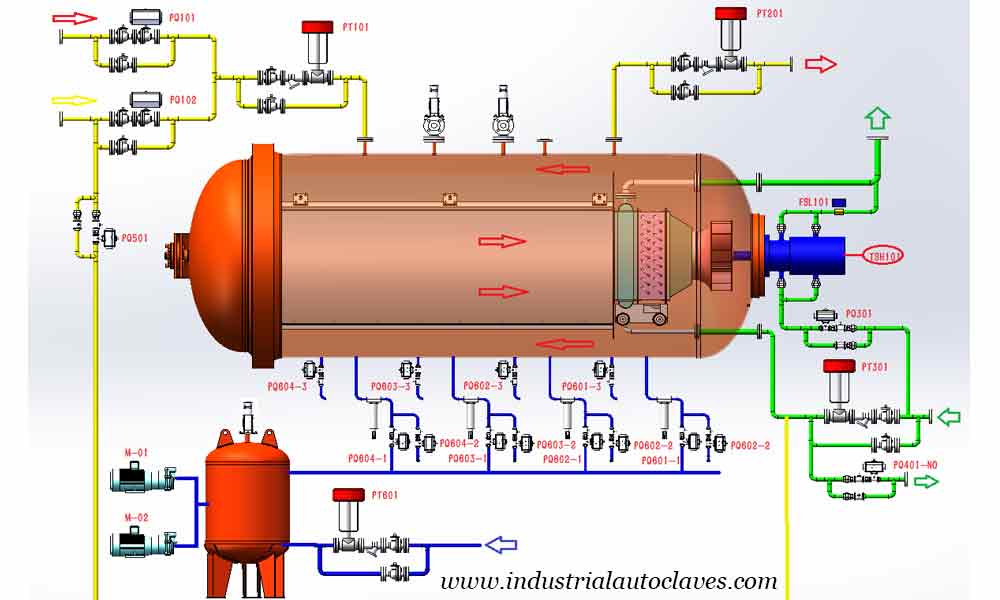
How to Operate Autoclave Composite
3.13 Temperature sensors location point and working scenes, view temperature distribution trend of mold
3.14 Simulation view scenes for simulate progress work going on to avoid accidents happened.
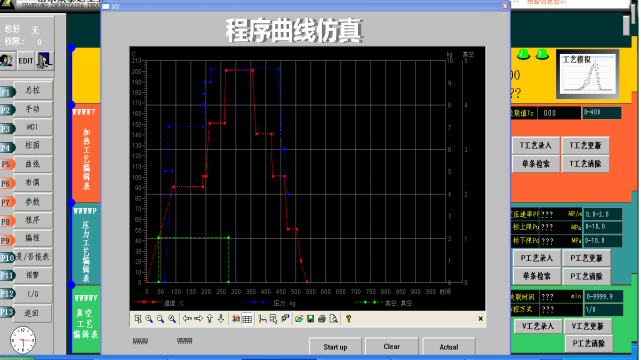
How to Operate Autoclave Composite
3.15 Immediate curve scenes to show all running trend interior of autoclave
3.16 Operation environmental of autoclave pressure vessel
1)100% environmental material non-toxic
Workable environmental 5~45℃, moisture ≤75%
3.17 Air supply unit of autoclave pressure vessel(customer-provided)
1)Air compressor : Exhaust pressure 1.0MPa, displacement 26m ³ / min, power 75KWx2
2)Cold and dry machine : Working pressure 1.0MPa, handling capacity 26m ³ / min
3)Filter : Filtration level 3, working pressure 1.0MPa, handling capacity 26m ³ / min
4)Buffer tank 2m³, design pressure 1.0MPa
5) Nitrogen machine 800m³ / h
6) Supercharger 4.0MPa 13m³ / h
7)Gas storage tank 4.0MPa 160m³
3.18 Circulating water unit of autoclave pressure vessel(customer- provided)
1)FRP cooling water tank 32000L, each volume 8000L
2)Auto water makeup valve
3)Conductivity sensor with auto‐makeup
4)Cooling water pump and its control, pump head 30m, flow 50m3/h
5)Closed cooling tower, throughput 50m3/h
6)Tower water pump and controls
- DUTY FOR BUYER AND SELLER
4.1 SELLER RESPONSIBILITY :
1) Alltheelectrical cables and wires connection between power cabinet, pressure vessel and all other autoclave subsystem.
2)Autoclave’s start-up and commissioning
3) Maintenance ( according to quotation in details)
4)Provide Spare Parts in 1 year by seller for free, exceed 1 year, the seller could supply but with extra cost.
4.2 BUYER RESPONSIBILITY:
1)The following items including materials will be provided by the customer:
2)Connect power cables to autoclave’s main circuit breaker
3)Assistant work for autoclave’s commissioning
3.1) Autoclave transport works inside buyer site.
3.2) Provide composite part as a sample for test at buyer site
5 . SELLER SITE CONFIRM
1)Autoclave will be tested, inspected, and accepted according to ASME Technical Specification.
2) TheInspectionReport of Autoclave will be provided after acceptance test.
3)Autoclave will be fully assembled and quality tested at the ASC Process Systems factory.
4)Equipment skid/platform is provided and integrated. The skid holds the control panel,power panel, cooling system, vacuum pumps, and so on.
5)100% quality testing and commissioning of autoclave at factory prior to shipping.
About STRENGTH Equipments
Taian STRENGTH Equipments Co., Ltd is the professional pressure vessel designer, manufacturer and exporter dedicated in supplying finest quality industrial autoclave, storage tank and dish head products and solutions to worldwide customer over 20 years. We have over 80 talented research and development experts, 2 million square meters manufacturing factory and more than 50 sets large-scale manufacturing machines. Our annual industrial autoclave and storage tank output can reach over 300 sets, dished head output can reach over 3000 sets.
STRENGTH Equipments is not only manufacturing high quality industrial autoclaves, storage tanks and dished ends but also providing custom product design, fabrication and after-sale service. ODM, OEM are also available. If you have any questions or inquiries, please fill and submit the following form, we will reply as soon as possible.