About manufacturing process of industrial pressure vessel( also called pressure vessel) mainly includes the preparation of raw materials. Such as marking, blanking, forming, welding, non-destructive testing, hydraulic testing, etc.
1.Preparation of Raw Materials
Steel must be pretreated before marking. Pretreatment of steel refers to the purification, orthopedic and protective primer of steel plates pipes and section steels.
Purification treatment is mainly to steel plate, pipe and section steel in the marking, blanking, welding processing. The steel after cutting, groove processing, forming, welding to remove the rust on the surface, oxide skin, oil and welding slag.
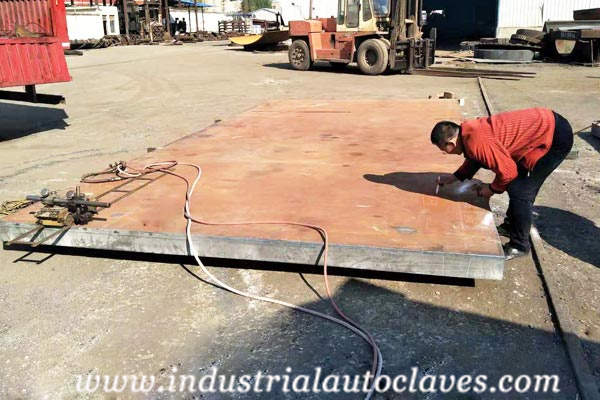
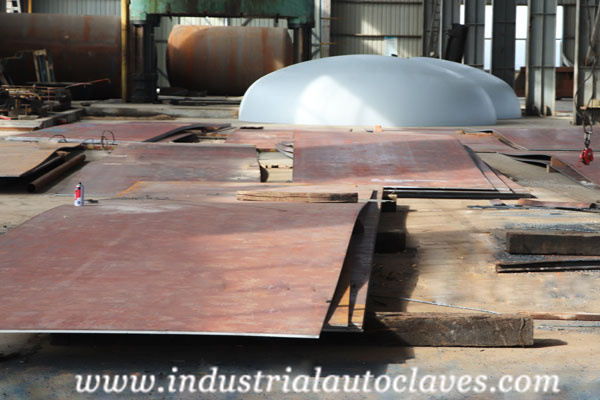
2.Marking
Marking is the first process of pressure vessel manufacturing process. It is directly determines the dimensional accuracy. Also geometric shape accuracy of parts after forming. In addition it has a great influence on the subsequent group and welding process.
The Marking is in the raw material or the initial processing of the blank on the marking line, processing line. All kinds of position line and inspection line. And mark (or write) the necessary signs and symbols. Usually, Marking process includes the parts of the unfolding, lofting and marking and other links. So the blank size should be determined before marking. Necessarily, the blank size is composed of the unfolded size of the part and various machining allowances.
3.Blanking
First, Blanking is also called cutting. It refers to the process of separating the required blanks from the marked raw materials. Generally, Cutting methods include gas cutting and plasma cutting.
Gas cutting is also called flame cutting, gas cutting belongs to thermal cutting, cutting requires a preheating flame. But only the flame can not achieve cutting. The key is to have high-speed pure oxygen flow.
Plasma cutting uses high-temperature, high-speed plasma flame flow to fuse materials to form incisions. It belongs to high temperature melting cut in thermal cutting. It is not restricted by physical properties. Plasma cutting can cut metals and non-metals. But it is mainly used to cut stainless steel, aluminum, copper, nickel and their alloys.
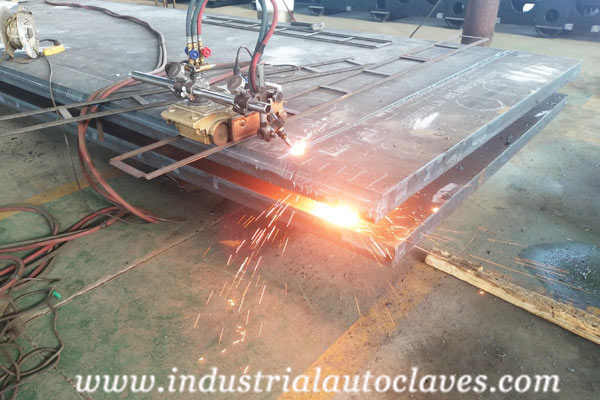
4.The Forming
The forming of shell
Shell is composed of several shell welded by circumferential welds. As well, the shell is welded by plate rolling (rolling) and longitudinal welds. It is the basic manufacturing method of shell. Next, the principle of rolling bending is to use a rolling machine to impose continuous. And uniform plastic bending of the steel plate to obtain a cylindrical surface.
Forming of Dished Head
There are three main forming methods of dished head: stamping, spinning and explosive forming. At present, the common methods are stamping and spinning.
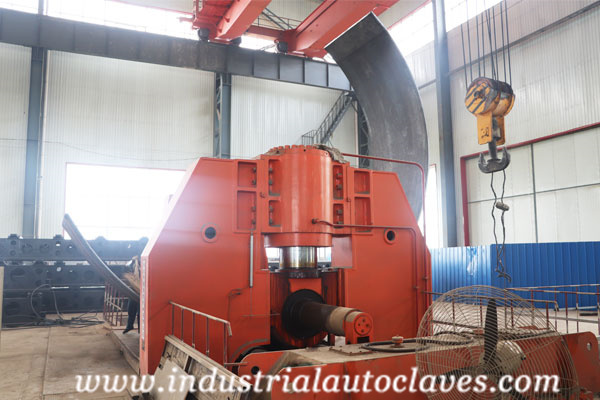
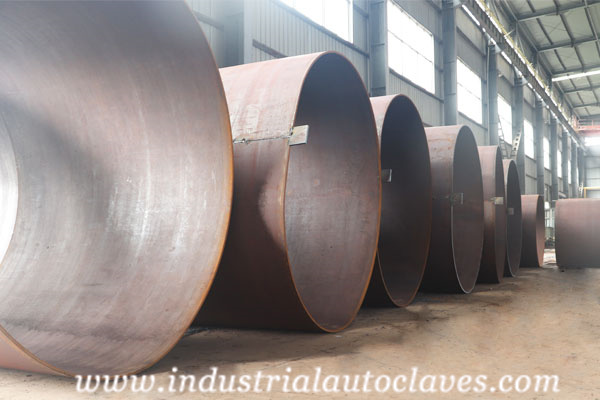
5.Welding
Welding is the process by which the atoms are joined together to form a permanent joint by heating, pressurizing, or both. Fusion welding is a processing method in which the workpiece to be welded is locally heated to melt. Furthermore condensed to form a weld to connect the components together. Including arc welding, gas welding, electroslag welding, electron beam welding, laser welding, etc. In fact, Fusion welding is a widely used welding method. Most low-carbon steels and alloy steels are welded by fusion welding.
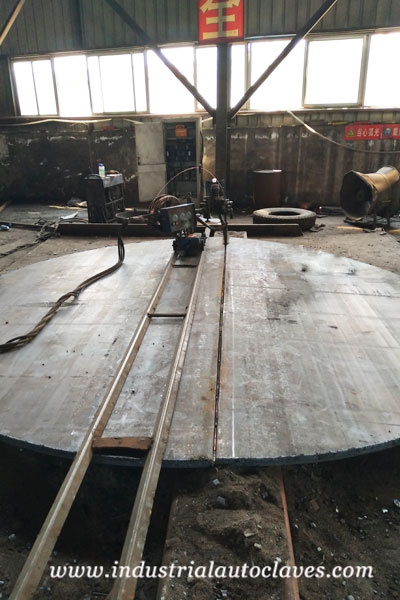
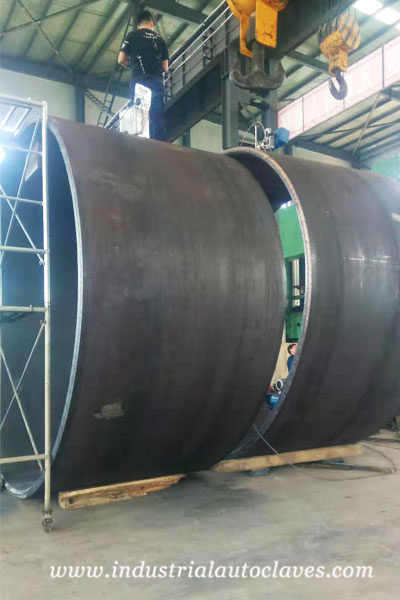
6.Nondestructive Testing
Nondestructive testing (NDT or NDE) is a technology that detects defects, chemical and physical parameters of materials. Parts and equipment using ray, ultrasonic, infrared, electromagnetic and other principles. Another technologies combined with instruments without damaging. Or affecting the performance of the object to be tested. For example, Radiographic examination (RT), ultrasonic examination (UT), magnetic particle examination (MT) and liquid penetration examination (PT) are commonly used.
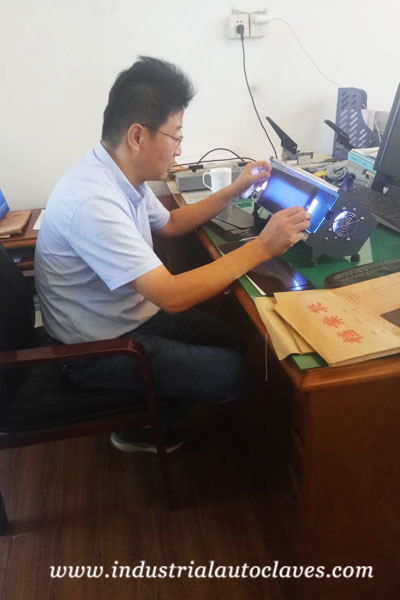
7.Hydrostatic Test
Hydrostatic test (overpressure pressure test) is one of the important means of industrial pressure vessel inspection. By filling and pressurizing the industrial pressure vessel. The shell, dished head, accessories of the pressure vessel are inspected during and after pressurization. Whether the material of the pressure component and the weld are infiltrated and cracked. And whether plastic deformation is visible to the naked eye under the test pressure. In brief, main purpose is to check the compressive strength of the pressure parts. Effectively, it can avoid accidents caused by the damage of the pressure parts. Defects that are not easy to be found in operation. Check the pressure parts and their welds, expansion joints. And sealing surface(manhole,check hole, hand hole) flanges (or bolt) and other joints are tight, and whether there is leakage.
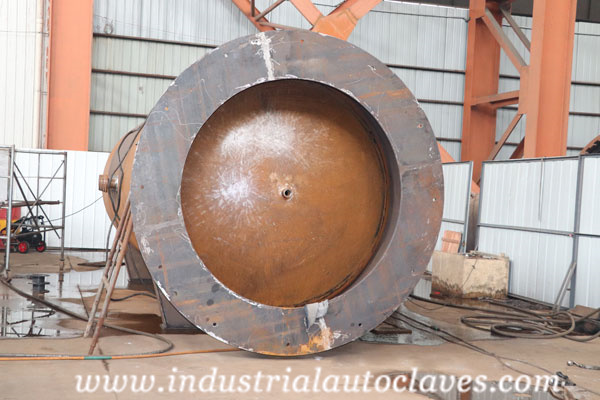
About STRENGTH Equipments
Taian STRENGTH Equipments Co., Ltd is the professional pressure vessel designer, manufacturer and exporter dedicated in supplying finest quality industrial autoclave, storage tank and dish head products and solutions to worldwide customer over 20 years. We have over 80 talented research and development experts, 2 million square meters manufacturing factory and more than 50 sets large-scale manufacturing machines. Our annual industrial autoclave and storage tank output can reach over 300 sets, dished head output can reach over 3000 sets.
STRENGTH Equipments is not only manufacturing high quality industrial autoclaves, storage tanks and dished ends but also providing custom product design, fabrication and after-sale service. ODM, OEM are also available. If you have any questions or inquiries, please fill and submit the following form, we will reply as soon as possible.