There are five important factors should be considered in the selection of composite curing autoclave. The 5 factors are listed as followed.
Ⅰ. Expected Maximum Product Size;
Ⅱ. Resin System of the Product;
Ⅲ. Properties of Resins;
Ⅳ. Mold Design;
Ⅴ. Production Cycle
Ⅰ. Expected Maximum Product Size
When customers plan to purchase composite curing autoclave, they will inevitably estimate the size of the composite autoclave. They usually want to reserve some and purchase larger composite curing autoclave as far as possible under the premise of site and fund.
Customers need to consider the size of the mold according to the size of the composite autoclave. Because the composite curing autoclave depends on the circulation of air to heat the mold, therefore, we must fully consider the flow of air channel, and not blockage the tank space. However, you do not blindly choose a large size model, by China’s road transport bridge height restrictions, the outer diameter more than 4m is difficult to transport, corresponding to the effective use of composite curing autoclave diameter of about 3.5m. Below this size, the composite curing autoclave can be manufactured in the factory and transported to the installation site, the construction cycle is short. Above this size, you need to carry on the spot fabrication, the construction cycle is long, the cost is high. At the same time, the composite curing autoclave has high energy consumption, which requires comprehensive consideration of the scale of the plant and the power distribution capacity.
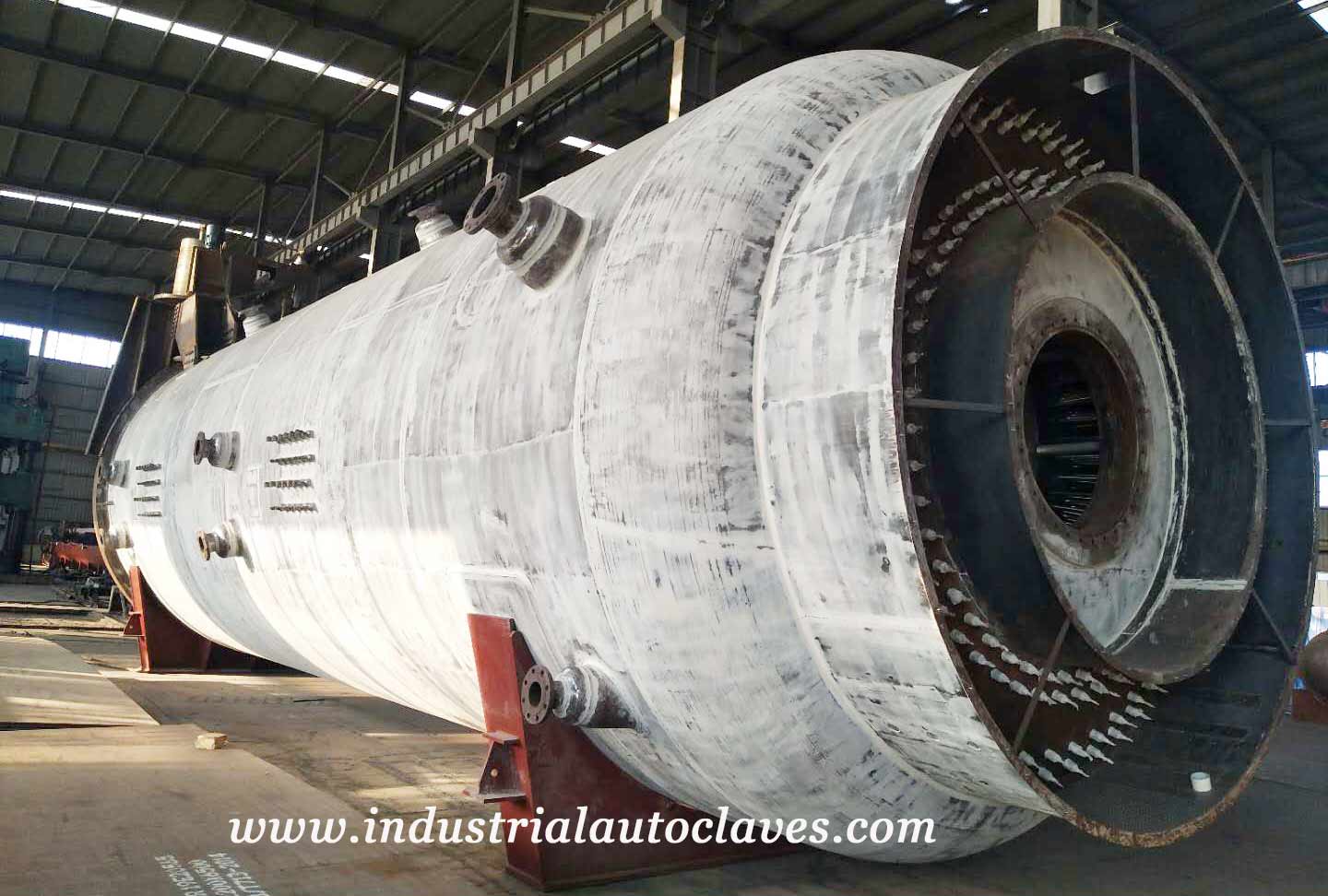
Ⅱ. Resin System of the Product of composite curing autoclave
The performance requirements of composite curing autoclave for forming composite materials mainly depend on the resin system used. Among the commonly used thermosetting resins, epoxy resin and phenolic resin are the most widely used.
Epoxy resin covers covering a wide range from room temperature curing to high temperature curing according to different formulations. However, the performance of room temperature curing and low temperature curing resin is not suitable for the use of composite curing autoclave process. The curing temperature of epoxy resin commonly used in composite curing autoclave process ranges from 120℃ to 180℃. Generally, the curing pressure of epoxy resin system is 0.6m Pa, which can stabilize the mechanical properties and meet the requirements after curing. The pressure can be increased appropriately if the shape is complex.
Phenolic resin system is also widely used, the oven curing phenolic resin system effect can meet the requirements of the application of low, but the composite curing autoclave should be applied when the requirements of higher fiber volume content, higher density, lower defects. The curing temperature of phenolic resin system is usually from 120℃-170℃, and the curing pressure is from 0.4mpa-2mpa according to the different formula and material performance requirements.
For the users of the autoclave with epoxy resin and phenolic resin system, the curing auxiliary materials are conventional nylon film vacuum bag, non-woven breathable felt and vacuum sealing tape are supplied on the market. The upper limit of short-term temperature resistance of these materials is usually between 170℃ and 200℃. Therefore, for these users, the use of industrial autoclave rated operating temperature above 200℃ is not meaningful. Composite curing autoclave manufacturers usually design the internal heat resistant structure according to 250℃, if the user can accurately provide the maximum operating temperature, autoclave manufacturers can accurately calculate the heating load, reduce the installed power, to achieve the effect of energy saving.
There are many kinds of resin systems used in composite materials, and some high performance resins are used in a small range, only in aerospace, electronics and other high end fields, such as high temperature resistant bisma resin, polyimide resin, cyanoate resin with high dielectric properties. The hot melt resin system being researched and developed is expected to greatly reduce the manufacturing cost of composite materials and improve the manufacturing efficiency.
The composite autoclave with the highest operating temperature of 250℃ can meet the curing temperature requirements of bisma resin and cyanoate resin. Generally, the pressure of 0.6mpa can meet the requirements of mechanical properties. If other properties are required, the pressure may need to be further improved. However, for the auxiliary materials used in the curing of these two composite materials, the reliable temperature resistance is about 230℃, which greatly restricts the process.
Polyimide resin is the current practical temperature resistance grade of the highest resin, curing temperature can run in the 300-370℃, and has a further trend to improve, and the curing pressure requirements of 1.5mpa, or even more than 2mpa. This requires a high temperature and high pressure hot pressure tank. High temperature and high pressure composite curing autoclave has great difficulty in the technology, at the same time, the level of heat-resistant materials auxiliary manufacturability is poor, it is difficult to guarantee the sealing of the vacuum bag, therefore, high temperature and high pressure autoclave must form a complete set of the nitrogen supply system to guarantee the process of internal atmosphere oxygen content of ≤8%, to put an end to materials used in the fire, it is recommended to use more than 95% purity nitrogen pressure.
Composites for hot-melt resin systems are being developed for applications such as automobiles. At present, the resin has not been widely used in the ongoing innovation, therefore, how to match the composite autoclave has not yet mature parameters. From the analysis of the law of material properties, the molding temperature of hot melt resin must be higher than the temperature of use, the lowest viscosity of hot melt resin can not be lower than the lowest viscosity of thermosetting resin. From the above two points of analysis, the temperature and pressure requirements of the hot pressure tank applied to the hot melt resin system should be slightly higher than that of the conventional hot pressure tank. At the same time, the important goal of hot melt resin research is to achieve efficient molding, so there are corresponding requirements for equipment, which needs to be engaged in material and process researchers to further explore.
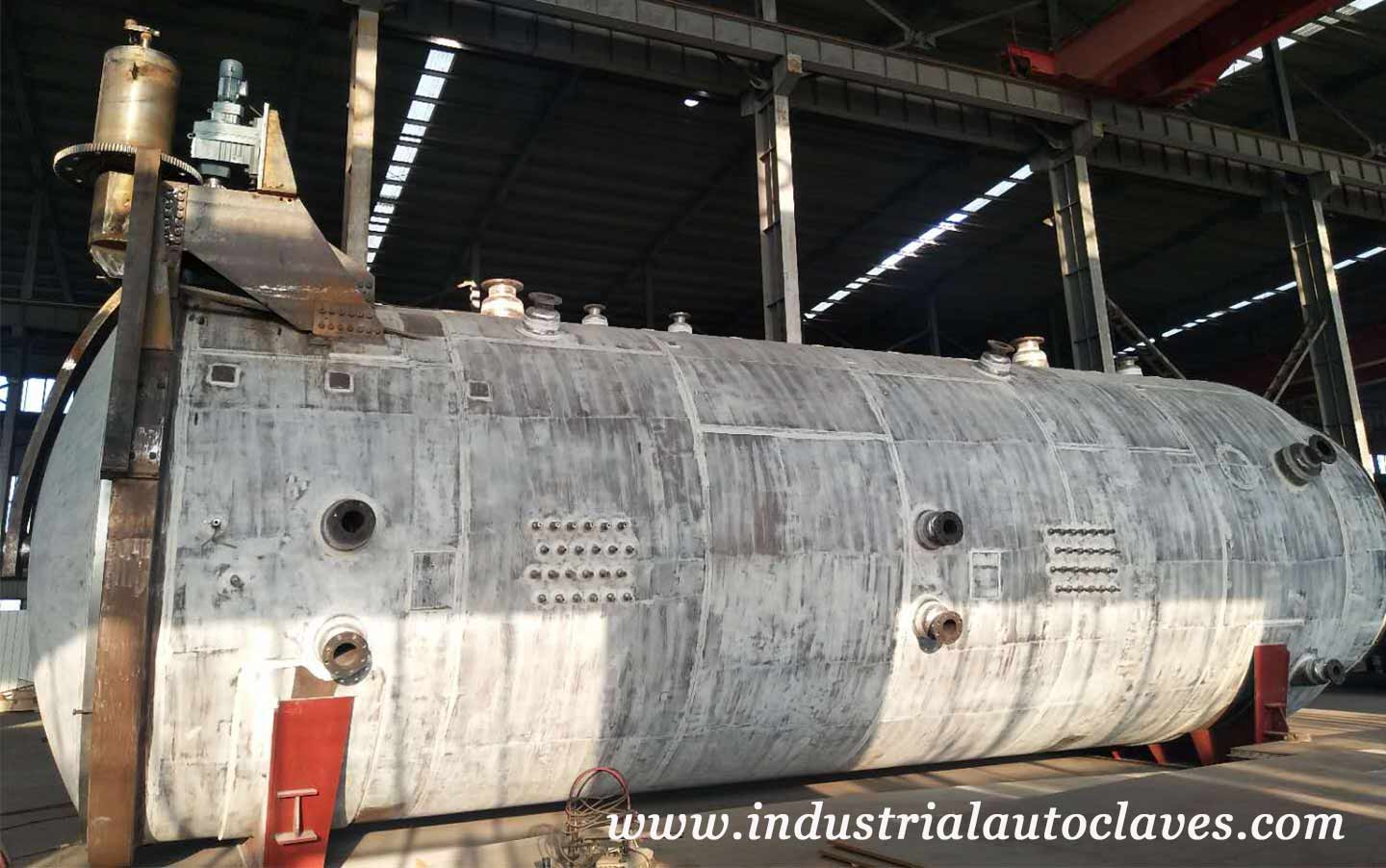
Ⅲ. Resin Properties
The performance of resin plays an important role in the design of composite curing autoclave pressurization system. The key to determine the final quality of the composite autoclave is what kind of temperature curve used in the curing process and when to pressurize.
① Epoxy resin, curing temperature: 120℃-180℃, working pressure is 0.6mpa.
② Phenolic resin, curing temperature: 120℃-170℃, working pressure is 0.4mpa-2.0mpa.
③ Double horse resin, curing temperature: 230℃, working pressure is below 0.6mpa.
④ Cyanate resin, curing temperature: below 230℃, working pressure is below 1.0mpa.
⑤ Polyimide resin, curing temperature: 300℃-370℃, working pressure is 1.5mpa-2.0mpa.
⑥ Hot melt resin, curing temperature: to be determined, working pressure is to be determined
The fluidity of the resin during curing determines the design method of the pressurization system to be equipped with the composite curing autoclave. If the flow of the resin can be controlled very well, not excessive outflow, then the pressure machine requirements are not high, good resin can achieve “beginning pressure” to heat and pressure. For composite products with this resin characteristics, the pressurization system design of the composite curing autoclave is allowed to be relatively simple. Air compressor can be used to pump directly into the tank, then eliminate the large gas storage tank which can reduce the equipment cost. However, when the composite curing autoclave specification is large, the need for supporting high-power air compressor, power distribution requirements, and comprehensive cost need to be calculated according to the specific situation.
If the flow of resin is too large, the pressure timing must controlled to complete the pressure at a certain point in a short period of time. In this case, the design of the composite curing autoclave pressurization system needs to be equipped with a large gas storage tank, which has very high requirements on the control system of the composite curing autoclave. The software of the hot pressure tank is required to have the following basic functions:
① Should control mold temperature, not air temperature;
②Pressure control must be temperature associated with the following, to achieve pressure at a predetermined temperature point;
③ When there is a difference in the temperature of several molds in the composite curing autoclave, it is necessary to wait for each mold to enter the pressure window and then apply pressure, the pressure process should be fast.
The pressure is higher than 1.6mPa of composite curing autoclave, the cost will have a relatively significant increase. Pressure requirement is high, the weight of composite curing autoclave vessel increases accordingly, cost increases. At the same time, for the composite curing autoclave air compressor and other facilities to increase the specifications, resulting in the increase in construction costs. Therefore, for the user, it is very important to choose the common pressure, the manufacturing pressure must be slightly greater than the commonly used design, the design pressure for the design of the safety margin is commonly used pressure is the use of the actual user process according to the user’s common pressure of gas supply system, in use is reasonable and economical.
Note: Some composite autoclave products require high molding pressure in order to achieve special performance. Although in terms of pressure vessels, there is no limit. However, from the safety and economic considerations, the design pressure of composite curing autoclave is not appropriate to exceed 5 mPa, the difficulty of equipment manufacturing is increased, the cost is greatly increased, and the reliability is greatly reduced.Therefore, if the molding pressure of the composite material must exceed 3mpa, it is recommended to use the hydraulic autoclave for the larger parts and the hot press for the smaller parts.
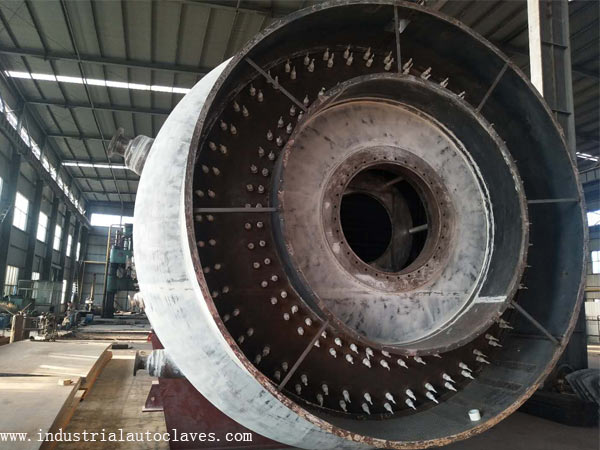
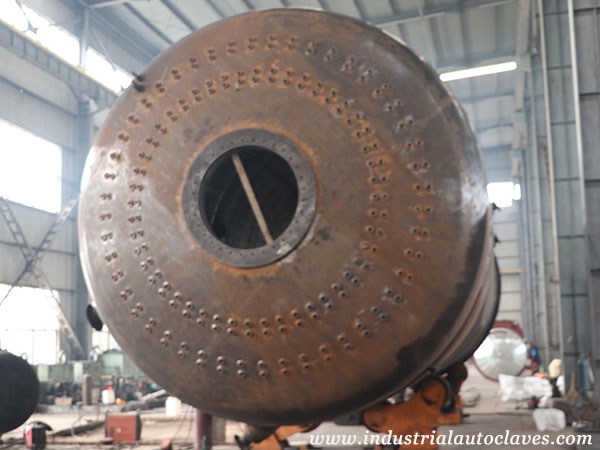
Ⅳ. Mold Design
There are many kinds of composite mold generally including composite mold, metal mold, metal mold and aluminum mold, steel mold, mold form according to the composite material manufacturers of product characteristics and process habits.The choice of mould form has an effect on the design of heating system of composite curing autoclave.
The heat capacity of composite mold is relatively small and is easy to heat up, but the lasting period is short, the accuracy is low. Metal mold has large heat capacity, slow temperature rise, long service cycle, high precision, composite curing autoclave to mold temperature rise, through the circulation of wind heat transfer.
For small size composite curing autoclave, due to the small size of the product, the difference is relatively small, in most cases do not need to consider too much, in order to shorten the process cycle, can require the composite curing autoclave no-load heating rate of 3-5℃/min. It is suggested to adopt 3℃/min, which requires too much to increase the installed power and increase the cost.
For large size composite curing autoclave, die temperature difference is not negligible, need to be calculated, in order to ensure that the die temperature difference in a certain range, can only reduce the mold heating rate.Therefore, in actual production, the heating rate of large size product molds is generally about 30℃/h.Therefore, the high no-load heating rate required by large size composite curing autoclave is meaningless, which greatly increases the construction cost.
Ⅴ. Production Cycle
Compared with other composite molding equipment, composite curing autoclave has the best comprehensive performance, the greatest adaptability, the best process control ability and the relatively low mold cost, so it is widely used in the composite industry. However, composite curing autoclave also has great limitations, such as high energy consumption, low molding efficiency.
The production time requirement determines the vacuum of the composite curing autoclave and the number of thermocouple channels. Production time requirements are high, at the same time the tank mold, vacuum and thermocouple channel requirements. However, if too many channels are required, the equipment cost will increase greatly, the failure rate will increase, and the maintenance cost will increase, which requires reasonable calculation.
At present, the application range of composite materials is getting larger and larger, and the low cost and rapid manufacturing of composite materials has become an important direction of technological development. In addition to resin, mold and other technical factors, curing equipment is an important link in the realization of low cost rapid manufacturing.
Most of the properties of the resin, when the heating rate is increased, the lowest viscosity has a decreasing trend, which is beneficial to the forming quality of composite materials. Some varieties of resins (such as polyimide) are so different that the more defects the product has, the lower the performance under the conventional hot pressing process. However, under the rapid heating process, high quality can be achieved.
The application of composite materials in automobile is a major direction of the development of composite materials technology and a major driving force of the development of composite materials technology. Automobiles are currently made of steel, the production efficiency is very high, known as the “one minute process” to replace metal composite materials, production efficiency is the first.
In order to achieve efficient production, there are many technical directions, including thermosetting resin, thermoplastic resin, RTM, molding, non composite curing autoclave technology and so on.
Our company aims at the development direction of technology, analyzes the advantages and disadvantages of each direction, think that composite curing autoclave technology, as long as it can solve the problem of energy consumption and molding cycle, still has great advantages, strong adaptability, reliable quality, low mold requirements.
The improved composite curing autoclave rapid prototyping technology developed by our company has the following characteristics:
① Curing of medium and low temperature resin can be completed within 30min-1h;
②Can shorten the curing and molding cycle of high temperature resin from about 20 hours to 3-5 hours;
③More than 90% energy saving than traditional composite curing autoclave;
④After curing, the mechanical properties of the material are the same as that of the traditional composite curing autoclave, and some states can be slightly improved.
About STRENGTH Equipments
Taian STRENGTH Equipments Co., Ltd is the professional pressure vessel designer, manufacturer and exporter dedicated in supplying finest quality industrial autoclave, storage tank and dish head products and solutions to worldwide customer over 20 years. We have over 80 talented research and development experts, 2 million square meters manufacturing factory and more than 50 sets large-scale manufacturing machines. Our annual industrial autoclave and storage tank output can reach over 300 sets, dished head output can reach over 3000 sets.
STRENGTH Equipments is not only manufacturing high quality industrial autoclaves, storage tanks and dished ends but also providing custom product design, fabrication and after-sale service. ODM, OEM are also available. If you have any questions or inquiries, please fill and submit the following form, we will reply as soon as possible.